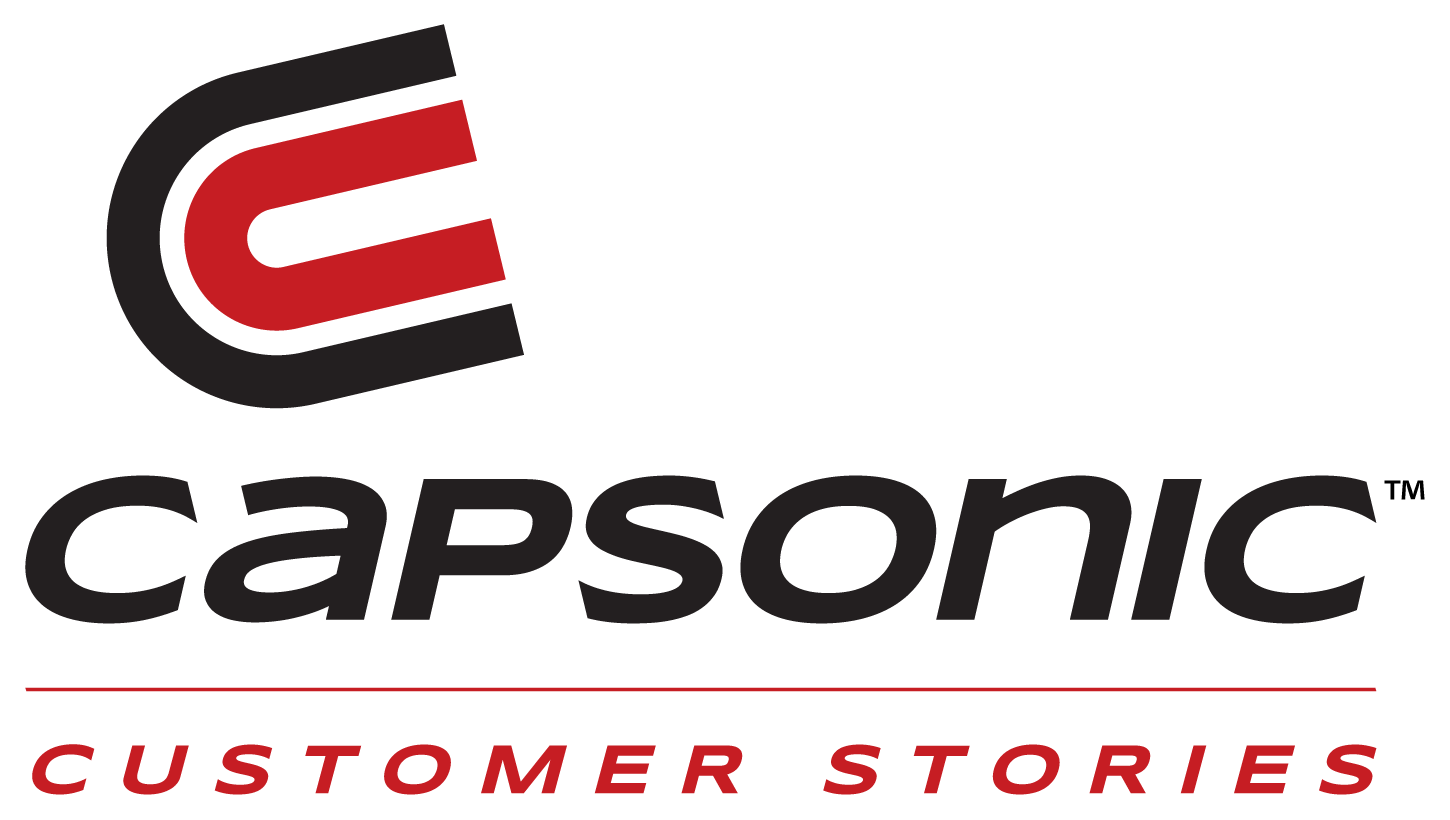
Fulfilling the Promise of Electrification Faster
CUSTOMER STORY
Charging Up for the Future
The rush to meet the growing demand for electric vehicles is on. Significant year-over-year sales increases for EVs, and big announcements by major automakers around plans to electrify much of their lineups by 2025 means the need for innovative manufacturing in Automotive has never been more pressing. Suppliers who can create lighter weight parts that also take up less space and increase horsepower in the process are among the unseen heroes moving the world toward lower carbon emissions.
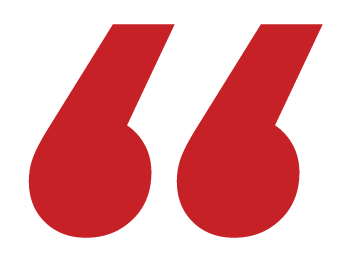
Capsonic developed new techniques to combine critical Automotive parts using plastic instead of metal in order to make them 50% lighter.
The quest to find industry leading solutions to the challenges presented by the EV revolution began a number of years ago at Capsonic. That’s when one of the largest Automotive parts makers worldwide found itself struggling in the prototype phase as it sought to produce new lighter weight components for the steering, brakes, and throttle bodies it was creating for electric cars and hybrid vehicles.
Fortunately, the engineering and manufacturing teams at Capsonic already had years of experience under their belts successfully developing advanced ways to use insert molded plastic for a number of industries. Working collaboratively with the Automotive parts maker’s team, Capsonic developed new techniques to combine critical Automotive parts together using plastic instead of metal to make them 50% lighter. These zero defect precision parts are also robust enough to handle the wear and tear they must face during everyday use in the electric motors, in the electric vehicles they are part of.
Another one of the keys to Capsonic’s ongoing success with this customer has been its ability to make everything happen in one-stop fashion at its facility in Juarez, Mexico. Being able to complete the electronic and assembly portions as well as the custom insert molding all under one roof, and then ultimately deliver a fully finished component to the customer, resulted in a 6-week lead time reduction, 30% inventory reduction, and a 25% cost savings.
Capsonic and its industry leading customers to this day continue to push the envelope on how they can create smaller, lighter weight components as together they seek to increase fuel economy for hybrid vehicles, and increase the range that EVs can go on a single charge. The future is now when it comes to EV innovation, and Capsonic is working ahead of the curve to lead the automotive industry forward with next generation solutions.
previous story:
Creating an Advantage in Aerospace Through a Superior Supply Chain
next story:
Moving Money Around the Globe Using a World-Class Precision Part for ATMs
Contact
Locations
Texas
7B Zane Grey St., El Paso, TX 79906
Mexico
6551 Hermanos Escobar Parque Industrial Magnaplex, Juarez, Chihuahua, Mexico 32320