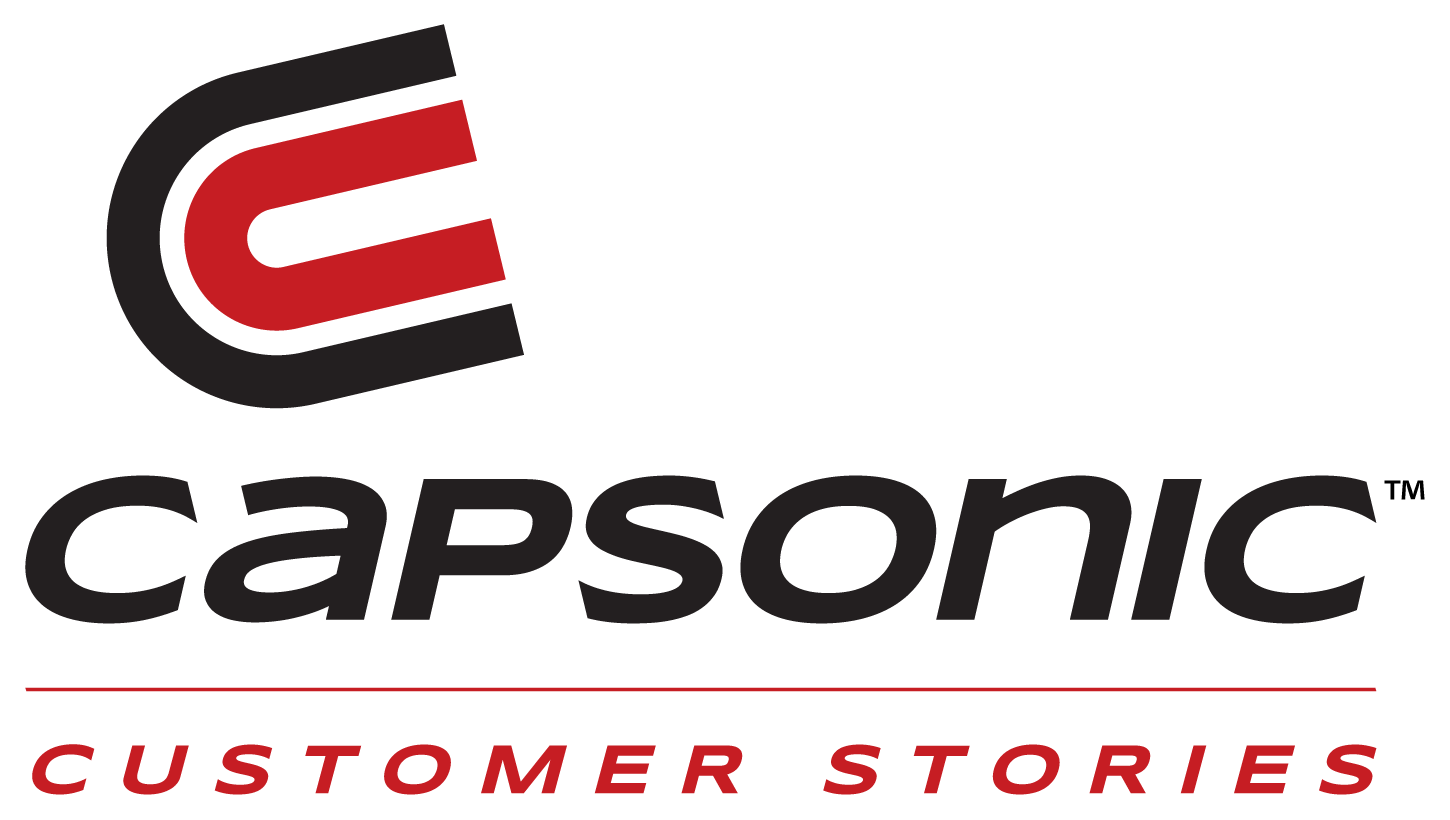
A Tale of Two Transfers
CUSTOMER STORY
Japanese OEM Seeks a New Home Base for Parts in America’s Heartland
When one of Japan’s top Automotive original equipment manufacturers (OEMs) had to relocate production of a key electrical window motor part to the United States, so that it would no longer have to be imported, expectations were high. A supply partner who could manufacture parts the same way they did in Japan with quality, pride, and a zero defect mentality was going to be key to a successful transition.
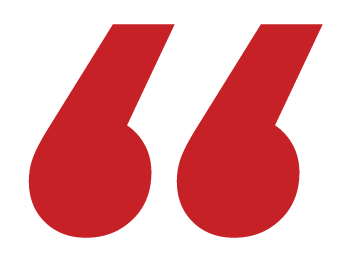
It was a big ask, and one that only a company with Capsonic’s level of expertise in insert molding and electromechanical assembly could handle.
Unfortunately, things quickly became complicated when it came to light that partner #1 was not up to the challenge. Finding a new manufacturer in the United States who could quickly ramp up and replicate the same kind of top quality parts became a quest that had millions of the U.S.’s highest selling vehicle makes and models hanging in the balance in production.
Pressure to Produce Under a New Roof
In essence, the challenge was to transfer an entire high-volume Japanese factory, and mindset around methodically pre-empting problems with failure prevention checklists. And, to do all of this while not losing pace. Moving existing production programs had to be done swiftly and accurately so as to not interrupt major OEM lines.
It was a big ask, and one that only a company with Capsonic’s level of expertise in insert molding and electromechanical assembly could handle. The Japanese manufacturer chose Capsonic over the competition because it could demonstrate that it both had the ability and capacity to take on this existing business, and it could exhibit that it had the guidelines and procedures in place that proved the experience necessary to make it happen the right way.
Moving Excellence Forward
The successful move itself was an exercise in teamwork, and making sure all lessons learned along the way were taken into consideration. It happened seamlessly over a weekend with Capsonic’s Transfer Program Checklist at the center of this huge victory.
To this day, many of us on the road have this key collaboration to thank for our ability to raise and lower the windows on our cars without having to think twice. The Japanese OEM is still a Capsonic customer some 20 years into the relationship with millions of dependable, high quality parts a year being supplied.
The key lesson in this tale remains that if suppliers are not meeting goals, or they are not developing facilities that logistically make sense to the customer, then programs can be successfully moved thanks to the kind of transfer protocols and proficiency Capsonic has in place to make it work.
previous story:
Manufacturing Reliable Aerospace Parts While Delivering Outstanding Efficiencies
next story:
Collaborating with Customers on Design
Contact
Locations
Texas
7B Zane Grey St., El Paso, TX 79906
Mexico
6551 Hermanos Escobar Parque Industrial Magnaplex, Juarez, Chihuahua, Mexico 32320